Stahllexikon
Hardox 450
C*) | Si*) | Mn*) | P*) | S*) | Cr*) | Ni*) | Mo*) | B*) | ||
---|---|---|---|---|---|---|---|---|---|---|
Kaltband | max. | 0,18 | 0,25 | 1,30 | 0,015 | 0,004 | 0,10 | 0,10 | 0,04 | 0,003 |
Warmband & Quartoblech | max. | 0,26 | 0,70 | 1,60 | 0,025 | 0,010 | 1,40 | 1,50 | 0,60 | 0,005 |
Der Stahl ist ein Feinkornstahl. *) Vorgesehene Legierungselemente.
Hardox 450 ist ein gehärteter Verschleißstahl für vielfältige Anwendungen. Er kann durch Biegen umgeformt werden uns lässt sich problemlos schweißen.
Härte (Garantierter Wert) |
HBW 425-475 (Quartoblech 3,2 - 80,0 mm Dicke) | |||||||||||||||||||||||||||||||||||||||||
Kerbschlagarbeit (Garantierter Wert) |
Prüftemperatur -40°C |
Kerbschlagarbeit Charpy-V in Längsrichtung mindestens 50 J |
||||||||||||||||||||||||||||||||||||||||
Streckgrenze (Typischer Wert, nicht garantiert) |
ca. 1.250 MPa | |||||||||||||||||||||||||||||||||||||||||
Lieferzustand | Gehärtet und angelassen | |||||||||||||||||||||||||||||||||||||||||
Wärmebehandlung | Hardox 450 ist für weitere Wärmebehandlung nicht vorgesehen. Die Eigenschaften können nicht aufrecht erhalten werden, wenn der Stahl Temperaturen über 250°C ausgesetzt wird. Hinweis: Für Anwendungen bei höheren Temperaturen bis zu 590°C empfehlen wir Toolox 44. | |||||||||||||||||||||||||||||||||||||||||
Oberflächen | Gemäß EN 10163-2 Klasse A, Unterklasse 1 | |||||||||||||||||||||||||||||||||||||||||
Ebenheit |
Toleranzen gemäß Hardox Ebenheitsgarantie Klasse D für Quartoblech, strikter als EN 10029. Für Warmband gemäß Hardox Ebenheitsgarantie Klasse A, enger als EN 10051, für Kaltband gemäß Hardox Ebenheitsgarantie Klasse B.
Angegeben ist jeweils die Ebenheit, gemessen in mm an einem 1-m-Lineal. Hinweis: Toolox 44-Quartobleche erfüllen engere Ebenheitsanforderungen für Dicken von 5,0-7,9mm = 4mm/1.000mm, 8mm/2.000mm und 8,0-99,9mm = 3mm/1.000mm, 6mm/2.000mm |
|||||||||||||||||||||||||||||||||||||||||
Schweißbarkeit |
![]() ![]() |
|||||||||||||||||||||||||||||||||||||||||
Biegen |
Die Biegbarkeit für Quartoblech entspricht der Hardox Biegegarantie Klasse E. Bandblech entspricht der Hardox Biegegarantie Klasse C für Kaltband und Klasse B für Warmband. Die Garantien entsprechen mindestens DIN EN 10025-6 und EN ISO 7438. Genannt ist das Verhältnis Biegewerkzeugradius/Blechdicke.
|
Ultraschallprüfung
Jedes Blech wird aufwendig geprüft, Zeugnisse 3.1 sind verfügbar, die internen Standards sind vielerorts strenger als der Industriestandard.
Oberflächenprüfung1)
Gemäß EN 10 160 |
Abstand zwischen parallelen Prüflinien [mm] | Zu beachtende minimale Fehlerfläche [mm²] | Maximal zulässige Fehlerfläche [mm²] | Maximale Anzahl lokaler Fehler [Anzahl/m²] | Entsprechende Stahl-Eisen- Lieferbedingungen |
---|---|---|---|---|---|
- | 100 | 1000 | 10000 | 1 | SEL 072 Klasse 5 |
S0 | 100 | 1000 | 5000 | 20 | - |
S1 | 100 | 100 | 1000 | 15 | SEL 072 Klasse 3 |
S2 | 50 | 50 | 100 | 10 | SEL 072 Klasse 2 |
S3 | 50 | 20 | 50 | 10 | SEL 072 Klasse 1 |
Randzonenprüfung2)
Gemäß EN 10 160 |
Randzonenbreite2) [mm] | Zu beachtende minimale Fehlerlänge [mm] | Maximal zulässige Fehlerlänge [mm] | Maximal zulässige Fehlerfläche [mm²] | Maximale Anzahl Fehler pro m Länge | Entsprechende Stahl-Eisen-Lieferbedingungen |
---|---|---|---|---|---|---|
E0 | 50 - 100 | 50 | 100 | 2000 | 6 | - |
E1 | 50 - 100 | 25 | 50 | 1000 | 5 | SEL 072 Klasse 3 |
E2 | 50 - 100 | 20 | 40 | 500 | 4 | SEL 072 Klasse 2 |
E3 | 50 - 100 | 15 | 30 | 100 | 3 | SEL 072 Klasse 1 |
E4 | 50 - 100 | 10 | 20 | 50 | 2 | - |
1) Die Prüfung kann bestellt und durchgeführt werden als Gesamtprüfung, beispielsweise E1S1 oder E2S2, oder als Nur-Randzonen oder Nur-Oberflächenprüfung, beispielsweise E1 oder S1.
2) Die Breite der Randzone bei der Randzonenprüfung variiert in Abhängigkeit von der Dicke des Blechs.
Die Dickentoleranzen der Bleche gemäß AccuRollTech™ sind enger als DIN EN 10 029.
Nenndicke [mm] | Hardox Toleranzklasse A [mm] | Maximaler Dickenunterschied im Blech [mm] | |||
---|---|---|---|---|---|
min | max | ||||
- | 4,9 | -0,3 | +0,4 | 0,5 | |
5,0 | - | 7,9 | -0,3 | +0, | 0,6 |
8,0 | - | 14,9 | -0,4 | +0,6 | 0,7 |
15,0 | - | 24,9 | -0,5 | +0,7 | 0,8 |
25,0 | - | 39,9 | -0,7 | +0,8 | 1,0 |
40,0 | - | 79,9 | -0,9 | +1,5 | 1,1 |
80 | - | -1,0 | +2,2 | 1,2 |
Hardox-Bleche haben eine erstaunliche Ebenheit.
3,2-3,9 | 4,0-4,9 | 5,0-5,9 | 6,0-19,9 | 20,0-130,0 | ||
---|---|---|---|---|---|---|
Hardox 450 | Quartoblech Klasse C Messlänge 1.000mm |
15mm | 7mm | 5mm | 4mm | 3mm |
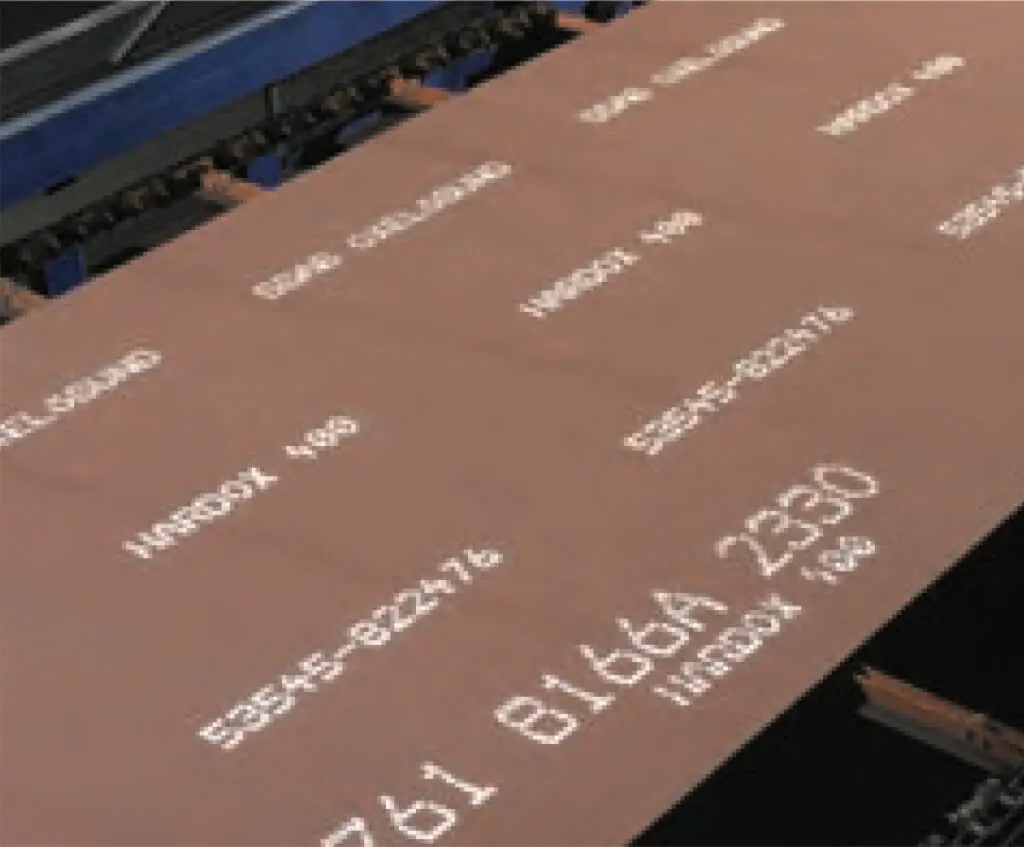
Bleche aus Hardox haben standardmäßig einen Rostschutzanstrich sowie eine Einzelblech-Kennzeichnung.
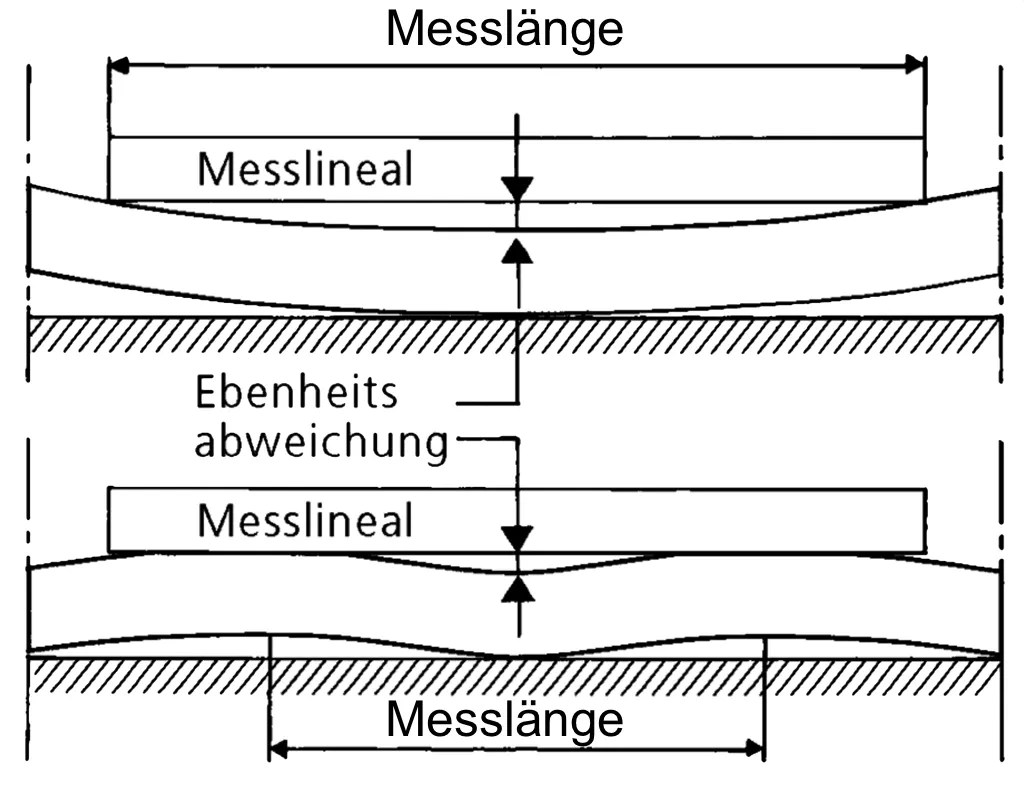
Schweißhinweise
Hardox verbindet einzigartige Verschleißfestigkeit mit hervorragender Schweißbarkeit. Alle üblichen Schweißverfahren können für Verbindungen von Hardox mit schweißbaren Stählen verwendet werden.
Für beste Schweißergebnisse achten Sie auf Trockenheit, Sauberkeit und Korrosionsfreiheit. Besonderes Augenmerk richten Sie auf die Auswahl des Schweißgutes, Temperaturen, Wärmeeintrag und die Fugengeometrie.
Niedriglegierte oder unlegierte Schweißwerkstoffe mit einer Zugfestigkeit von 500 MPa sind für Hardox und Toolox verwendbar. Hardox 450 in Dicken von 0,7 – 6,0 mm erlauben Werkstoffe mit Festigkeiten von 900 MPa. Niedrig legierte Werkstoffe ergeben eine höhere Härte, was die Verschleißfestigkeit begünstigt. Wenn die Verschleißfestigkeit der Schweißnaht ausschlaggebend ist, so kann man an das Aufschweißen einer Verschleißschutzschicht denken.
Schweißverfahren | DIN EN ISO-Einteilung |
---|---|
MAG / Massivelektrode | EN ISO 14341-A- G 38x EN ISO 14341-A- G 42x |
MAG / Fülldrahtelektrode | EN ISO 17632-A- T 42xH5 EN ISO 17632-A- T 46xH5 |
MAG / Metallpuler-Fülldrahtelektrode | EN ISO 17632-A- T 42xH5 EN ISO 17632-A- T 46xH5 |
MMA / Stabelektrode | EN ISO 2560-A E 42xH5 EN ISO 2560-A E 46xH5 |
UP Unter-Pulver-Schweißen | EN ISO 14171-A- S 42x EN ISO 14171-A- S 46x |
WIG | EN ISO 636-A- W 42x EN ISO 636-A- W 46x |
niedrig- oder unlegierte Zusätze
Rostfreie Schweißzusätze können für alle Hardox-Stähle verwendet werden, für Toolox 44 sollten diese bevorzugt werden. Sie erlauben das Schweißen bei 5 – 20°C ohne Vorwärmung, außer bei Hardox 600 und Hardox Extreme. SSAB empfiehlt die folgenden Werkstoffe, die eine Streckgrenze von 500 MPa ergeben.
Schweißverfahren | DIN EN ISO-Einteilung |
---|---|
MAG / Massivelektrode | EN ISO 14343-A: B 18 8 Mn/ EN ISO 14343-B: SS307 |
MAG / Fülldrahtelektrode | EN ISO 17633-A: T 18 8 Mn/ EN ISO 17633-B: TS307 |
MAG / Metallpuler-Fülldrahtelektrode | EN ISO 17633-A: T 18 8 Mn/ EN ISO 17633-B: TS307 |
MMA / Stabelektrode | EN ISO 3581-A: 18 8 Mn/ EN ISO 3581-B: 307 |
UP Unter-Pulver-Schweißen | EN ISO 14343-A: B 18 8 Mn/ EN ISO 14343-B: SS307 |
WIG | EN ISO 14343-A: W 18 8 Mn/ EN ISO 14343-B: SS307 |
austenitische Zusätze
Als Schutzgas verwendet man beim Hardox-Schweißen grundsätzlich die selben Gase wie beim Schweißen niedrig- oder unlegierter Stähle.
Empfehlender Wärmeeintrag max.
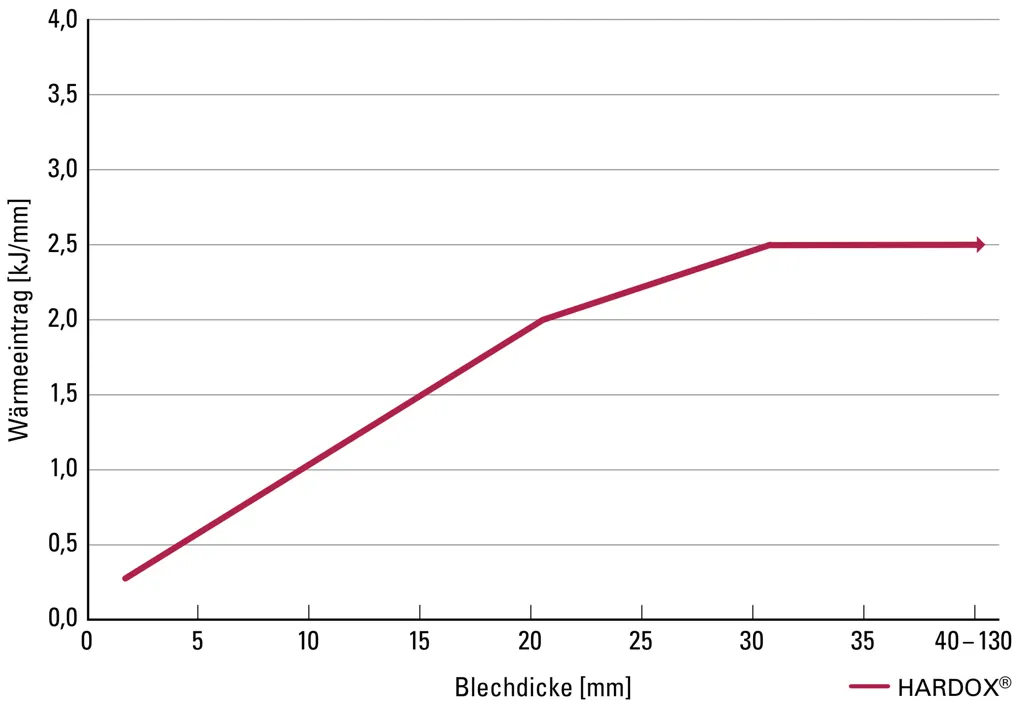
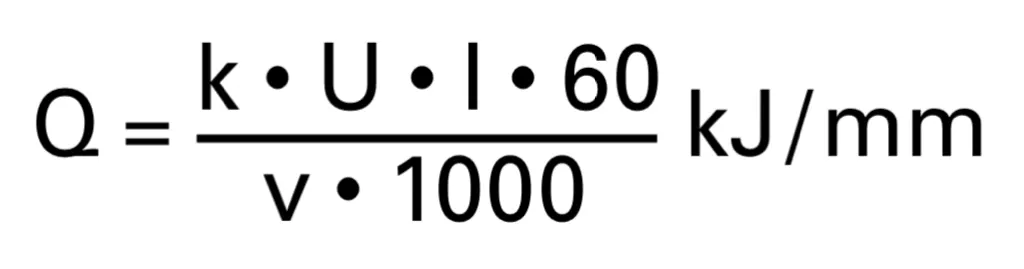
Wasserstoffgehalt
Die Gefahr der Wasserstoffversprödung ist wegen stählen.
Der Gefahr begegnet man zudem durch:
- Vorwärmen des Schweißbereichs
- Messung der Vorwärmtemperatur
- Verwendung von Schweißzusatzstoffen mit höchstens 5ml Wasser/100g
- Freihalten der Schweißfuge von Rost, Fett, Öl und Kälte
- Anwenden eines geeigneten Schweißverfahrens
- Vermeidung eines Schweißspaltes über 3mm an der engsten Stelle der Schweißfuge
Vorwärmung
Vorwärmung ist äußerst wichtig für eine gute Schweißnaht. Die empfohlenen Vorwärmtemperaturen zeigt die
nachfolgende Tabelle für niedrig- oder unlegierte Werkstoffe.
Bitte beachten Sie:
- Für Bleche unterschiedlicher Dicke orientieren Sie sich am dickeren Blech.
- Für unterschiedliche Blechwerkstoffe orientieren Sie sich an dem mit der höheren Vorwärmtemperatur.
- Für Wärmeeintrag unter 1,7kJ/mm erhöhen Sie die Temperatur um 25°C, unter 1,0kJ/mm orientieren Sie sich bitte im WearCalc-Programm.
- Bei niedrigen Außentemperaturen oder hoher Luftfeuchtigkeit erhöhen Sie die Temperatur um 25°C.
- Bei DV- oder DY-Nähten legen Sie die erste Raupe außerhalb der Blechmitte an.
Empfohlene Mindest-Arbeitstemperatur
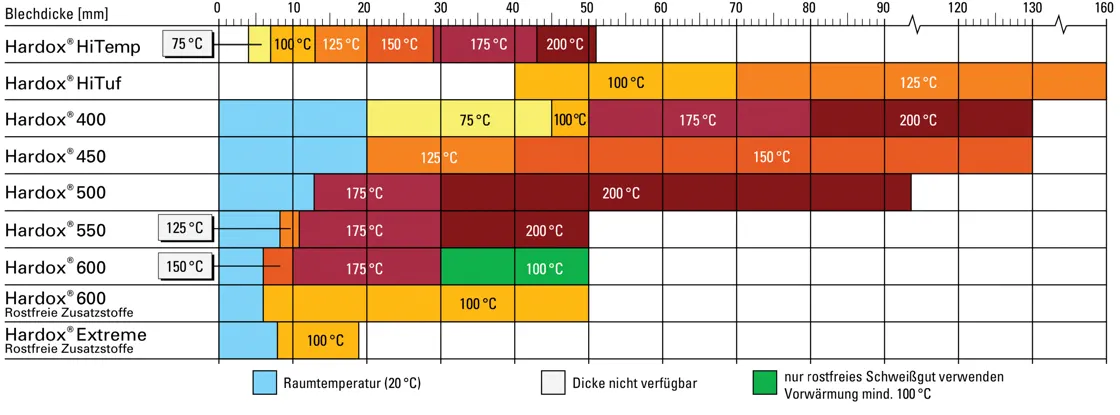
Die Höchsttemperaturen nach dem Schweißen einer Lage und vor Aufschweißen einer weiteren Lage sind:
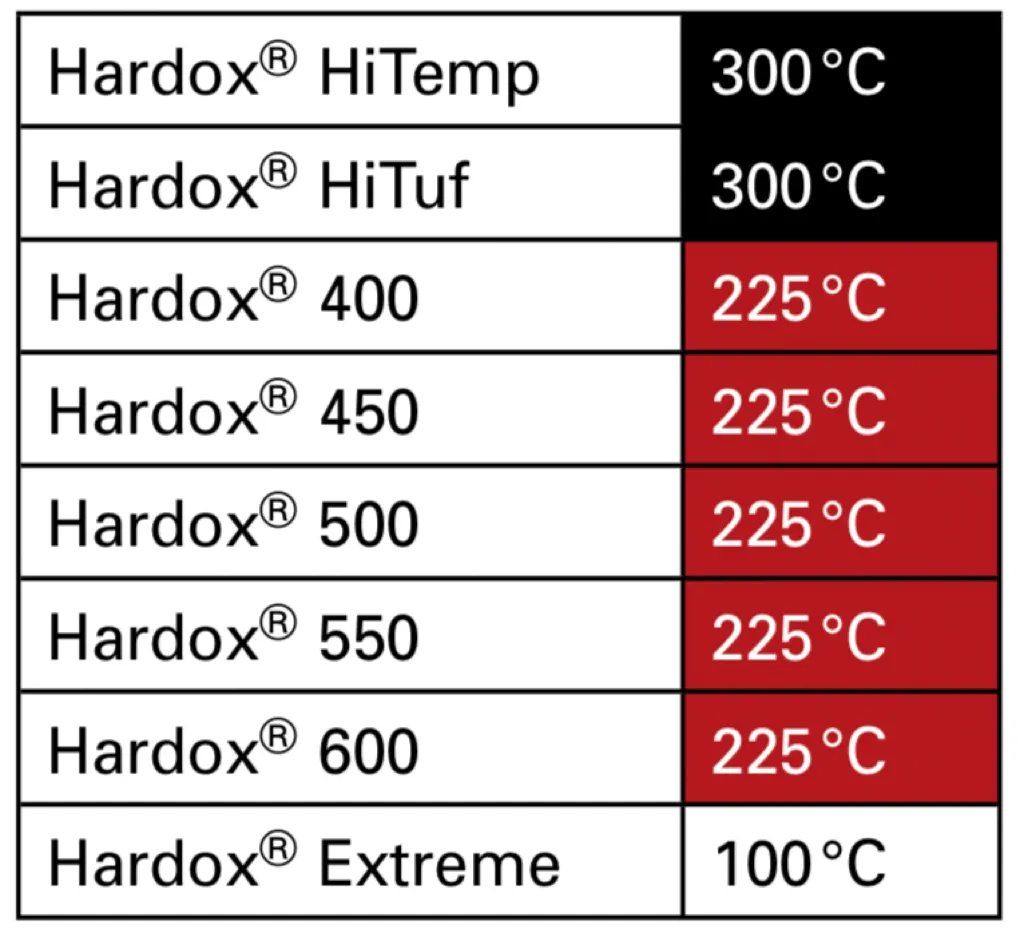

Es ist praktisch, die Temperatur an der Rückseite zu messen.
Dabei empfiehlt sich, etwa 2min/25mm Blechdicke abzuwarten.
Die Temperatur sollte ca. 75 – 150 mm beidseitig der Schweißfuge erreicht sein.
Grundierte Bleche
Durch den geringen Zinkgehalt kann direkt auf der Hardox-Grundierung geschweißt werden, gleichwohl ist es vorteilhaft, die Grundierung mit der Drahtbürste zu entfernen, um Porositäten zuvermeiden. Gute Belüftung ist wichtig für die Gesundheit des Schweißers und der Personen in der Nähe.
Wärmebehandlung
Eine Wärmebehandlung nach dem Schweißen ist nicht vorgesehen, um die mechanischen Eigenschaften von Hardox zu erhalten.
Härtevergleichstabelle für Toolox und Hardox
Zugfestigkeit MPa |
715 | 790 | 820 | 861 | 935 | 995 | 1011 | 1090 | 1169 | 1245 | 1328 | 1412 | 1494 | 1580 | 1758 | 1940 | 2130 |
Vickershärte HV |
205 | 233 | 243 | 261 | 289 | 311 | 317 | 345 | 373 | 401 | 429 | 458 | 485 | 514 | 569 | 627 | 682 |
Brinellhärte HBW |
225 | 250 | 260 | 275 | 300 | 320 | 325 | 350 | 375 | 400 | 425 | 450 | 475 | 500 | 550 | 600 | 650 |
Rockwell HRC |
19 | 22,5 | 24 | 26 | 29 | 32 | 32,5 | 35,5 | 38 | 40 | 42,5 | 44,5 | 46,5 | 49 | 52,5 | 55 | 57,5 |